What is hydrogen and why do we want to use it?
Hydrogen is the lightest and most abundant element in the universe. It also has almost 2.6 times higher energy density per kg than diesel or petrol. What this means is that a car running on 1 kg of hydrogen will have the same range as that given by 3 kg of diesel/ petrol (Figure 1). Only nuclear energy provides a higher energy density per kg than hydrogen.
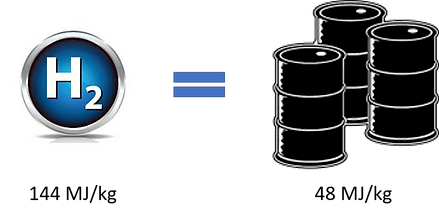
The dirty truth of current hydrogen production
90 million tonnes (Mt) of hydrogen are used annually in a myriad of industries including petrochemicals, fertilisers, steel, cement, semiconductors and the much talked about mobility. 40% of hydrogen is used in the petrochemical industry for making various chemicals and desulfurizing petrol and diesel. Another 40% of H2 is used for ammonia production, which is used as a fertiliser to produce 45% of the world’s food. Therefore, we can see that hydrogen is used at a massive scale in a bunch of very important sectors. The problem lies in the way this hydrogen is produced.
Almost 60% of the hydrogen we use is produced using a technique called steam methane reformation (SMR) in which methane and steam react with each other at high temperature to give carbon monoxide and hydrogen. The carbon monoxide is further reacted with water in a process called water gas shift reaction (WGS), which gives CO2 and hydrogen. The overall process of SMR + WGS releases 9 tonnes of CO2 per ton of H2 produced. Coal gasification which makes up almost 20% of hydrogen production is even worse, releasing 20 tonnes of CO2 per ton of H2 produced. This means over 900 Mt of CO2 is released every year, which is equivalent to the emissions of UK and Indonesia combined! This type of hydrogen with massive CO2 emissions is known as ‘grey hydrogen’. In order to reduce the impact of climate change and meet the pledges set in the COP26 meeting, it is crucial to replace grey hydrogen with a cleaner source of hydrogen production.
Clean hydrogen, ‘green’ hydrogen
Hydrogen produced using clean sources which have zero net CO2 emissions is known as ‘green hydrogen’. The most commonly used method to produce green hydrogen is water electrolysis. This is the process where an electric current is passed through water, thereby splitting it into its constituents, namely hydrogen and oxygen, as shown in Figure 2.
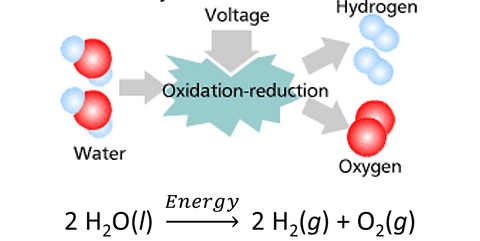
The electric current comes from renewable energy sources such as solar or wind energy. However, currently only about 0.03% of global hydrogen production is made by electrolysis. A major reason for this is the high cost of green hydrogen, which at $5-6/kg of H2 is 3-4x more expensive than grey hydrogen available at $1.5-2/kg. Consequently, there is a huge gap between the amount of clean hydrogen required and the quantity produced. In order to close this gap, we need to massively scale hydrogen production by electrolysis for which we need to solve a few critical problems.
Why is green hydrogen so expensive?
One of the major reasons for the high green hydrogen price is the high cost of the electrolyzer systems, which are the devices used for water electrolysis. Currently, most commercial electrolyzers are of two types- Alkaline water electrolyzers (AWE) and Proton exchange membrane electrolyzers (PEM). Other types of electrolyzers which are being introduced into the market are Anion Exchange Membrane electrolyzers (AEM) and solid oxide electrolyzers (SOE). Electrolyzers are extremely expensive, with capital costs in the range of $1000-2000/kW for AWE and PEMWE systems and >$2000/kW for AEMWE and SOE systems. This is very high when one compares it to the capital cost of solar cells ($300-500/ kW) or batteries ($150-200/kWh).
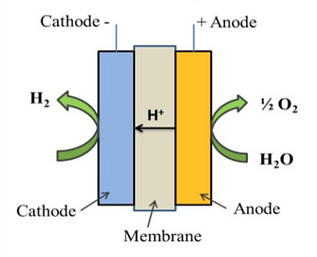
One of the major factors driving the high cost of electrolyzers is the price of the raw materials used to build them. Although there are several important components which go in an electrolyzer, the three critical components in current commercial electrolyzers are shown in Figure 3 and are: 1. The anode at which the water is oxidised to oxygen; 2. The cathode at which the water is reduced to hydrogen and; 3. The membrane which is used to keep the hydrogen and oxygen separate, while allowing a specific ion to pass through.
The price of these 3 materials alone can be 25-57% of the total manufacturing cost of the electrolyzer for PEMWE and AWE systems respectively. Hence, it is of vital importance to reduce the cost of the materials used in electrolyzers to bring down the cost of green hydrogen.
In the next post, we will discuss how the price of electrolyzers are influenced by the cost of the materials used in its components.
Newtrace is enabling wide-scale adoption of affordable green Hydrogen through their novel electrolyzer technology to help fight climate change and build a sustainable future for all. Follow us to stay informed about our updates!